Цех — довольно просторное помещение, где трудятся десятки рабочих. Все в одной комнате, разделенной габаритным оборудованием на несколько частей — по стадиям производства.
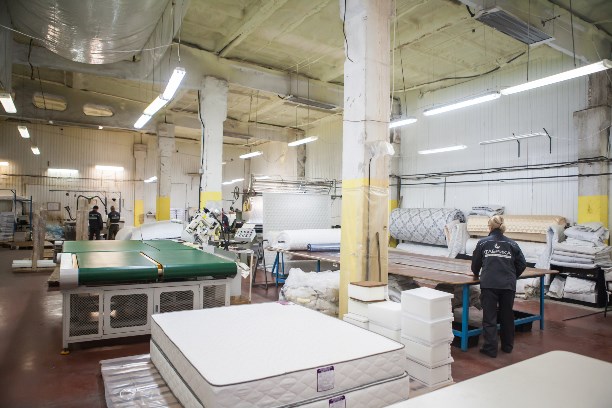
Вот так выглядит цех по производству матрасов.
В цеху — множество матрасов: здесь тебе и пышные комфортные гиганты, и полуторки, и скромные односпалки. Так и тянет поваляться!
Стоп. Тут время сказать о том, что толщина матрасов зависит от их состава. Чем больше материалов в основе, тем матрас выше (и по физическим величинам, и по классу). Так, например, на фабрике, где мы побывали, делают шесть видов матрасов: «Комфорт», «Стандарт», «Люкс», «Престиж», а еще беспружинные и детские. Этапы их производства схожи, единственное отличие — материалы. Но обо всем по порядку.
Самое главное в матрасе — пружинные блоки. Именно с их создания начинается «жизнь» каждого изделия. Есть два вида пружинных блоков: независимые и зависимые (такие двухконусные пружины, которые по форме напоминают песочные часы).

Зависимые пружинные блоки уже давно не пользуются популярностью.
Эту систему давно принято считать устаревшей: хоть она и экономична, но всё же ортопедические свойства в ней развиты, мягко говоря, слабо. Отдыхать на таких матрасах не так уж комфортно.
А вот из независимых пружинных блоков делают более 90% матрасов.
Блок представляет собой собрание маленьких, склеенных между собой пружинок цилиндрической формы. Их штампует станок: от оператора требуется лишь следить за корректной работой машины.

Сергей Новоженцев, оператор станка.
— Станок превращает обычную проволоку в спиралевидную деталь, — рассказывает оператор станка Сергей Новоженцев. — Навитые пружины укладываются в отдельные мешочки из нетканых материалов, упаковываются в чехол, а затем склеиваются.
На выходе получаются вереницы зачехленных пружинок — эдакая гусеница. Мы между собой называем эти детали «стаканами».
Затем цепочки попадают в «руки» следующего станка, он-то и делает из них блоки, склеивая «стаканчики». Мастер следит за тем, чтобы всё было по инструкции. Вокруг его рабочего места сотни белых пластов — готовые пружинные блоки.
Здесь судьбы будущих матрасов расходятся: заготовки наполняются различными топперами (материалами) в зависимости от того, продукт какого класса задумывается.
От 5 до 15 минут (в зависимости от размера матраса) уходит на создание одного независимого пружинного блока.
Немного о топперах. В далекие времена, тысячи лет назад, люди наполняли тканевые мешки травой, соломой и листьями и так спали. Зато «начинка» была полностью натуральной. В современных матрасах тоже есть натуральная составляющая – кокосовая койра. Это природный материал из спрессованных кокосовых волокон, пропитанных натуральным же латексом.
В некоторые модели матрасов также добавляются струттофайбер, термовойлок, трикотаж, пенополиуретан. Чехол – это чаще всего ткань жаккард с объемной стежкой.
Все эти материалы поставляются на фабрику огромными пластами. Чтобы они соответствовали размерам пружинного блока, мастер разрезает их на специальном станке.
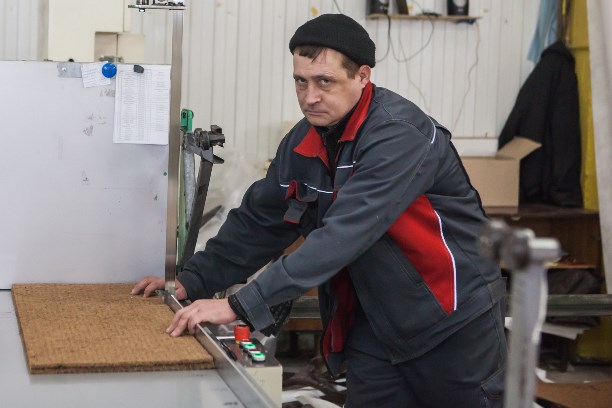
Процесс резки «начинки».
Рядом висит шпаргалка: в ней — точные размеры проектов и количество заказов.
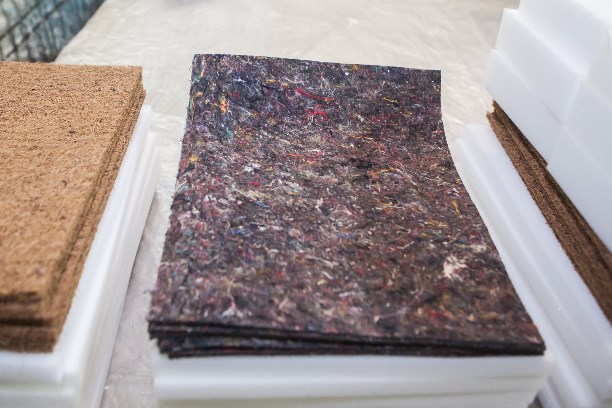
Вот так выглядят пласты после резки.
По сути, весь день сотрудника проходит за этим станком. Кладешь пласт на стол, режешь, относишь на формировку, и так раз за разом.
Формировка, можно сказать, — самая творческая работа здесь, на фабрике. Мастеру приносят уже отрезанные материалы и пружинный блок, а его задача — соединить их так, чтобы получился гармоничный параллелепипед.

Промежуточный этап работы.
Это сродни кулинарии: из сырых продуктов тебе надо создать аппетитное блюдо. Стол для моделирования — эдакая кухня для «приготовления» матрасов. Он вращается, что заметно облегчает работу мастерам.

Рабочее место формировщика.
— Мы работаем руками и глазами, — говорит формовщик Виктор Ковалев. — Мало просто подогнать детали под определенный размер — надо сделать это со вкусом. Ничего торчать не должно. Для верности одновременно работаем над одним матрасом вдвоем: кто-то занимается основной работой, кто-то контролирует. На один матрас в среднем уходит 20 минут.

Для удобства мастера работают на формировке в паре.
Убедившись в том, что материалы и пружины «встали в идеальную пару», мастера закрепляют результат. Надо сказать, что склейка – ювелирная работа: любое неаккуратное движение клеевого пистолета может загубить изделие.
И вот формировка завершена. Изделие уже приобрело очертания матраса: остались последние, но крайне важные штрихи. Направляемся к занятному оборудованию — огромному ткацкому станку, снабженному несколькими десятками катушек белых ниток.
Внизу, там, где работают механизмы, виднеются рулоны различных тканей.
— Для чего они? — спрашиваю. – Разве на обшивку нужно столько слоев?
— Это увеличивает срок эксплуатации, — рассказывает сотрудница фабрики Инна Шарипова. — Смотрите: все слои автоматически становятся единым целым, скрепляются. Раньше процесс выполняли люди: представляете, сколько это отнимало времени! Сейчас всё проще – нужно лишь следить за тем, чтобы нити и материал не запутались.
После моделирования матрас попадает именно сюда — в швейную зону. Первым делом он проходит этап стежки: машина наносит на наш «голый» параллелепипед три слоя ткани.
Сотрудницы ставят рулоны в машину — сначала спанбонд, затем синтепон, а сверху — обивочный материал. Именно в такой последовательности ткани наносятся на матрас.

Сотрудники цеха меняют тканевые рулоны собственноручно. Как, собственно, и нити.
На ленте уже красивый, «одетый» матрас выезжает к швеям.
Швеи доводят матрас до готовности. Они работают на окантовочных машинах — устройствах, отдаленно напоминающих огромные микроскопы.
Матрас кладут на стол, расправляют на нем все ткани, зажимают изделие «лапой» машины и жмут на кнопку.
И вот на матрасе автоматически появляются маленькие бортики.
Осталось лишь упаковать!
Упаковку также производит машина.
На пленку клеится этикетка с указанием класса, состава и даты изготовления матраса.
Всё, продукт готов! Матрасы отгружаются с фабрики и отправляются в магазины.
Приятных снов!
115 матрасов — столько в среднем производит тульская фабрика в день.
60 минут — примерно столько времени требуется на изготовление матраса среднего класса и величины.
13,5 см — высота стандартного пружинного блока.
256-330 пружин на кв. м — плотность стандартных матрасов.
Не менее 10 лет – срок эксплуатации большинства пружинных матрасов.
Благодарим «Фабрику современной мебели» за помощь в подготовке материала.